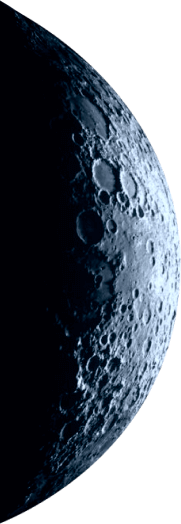
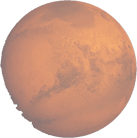
We are thrilled to share some major developments from the Copenhagen Suborbitals rocket shop. Over the years, we have built multiple large hybrid and liquid rocket engines, each time inching closer to our goal of sending amateur astronauts to space and back. Our aspirations are now more achievable than ever with significant progress on our speaker rocket project.
Our team has tirelessly worked on and tested our liquid oxygen and ethanol propellants. While the progress on the 100 kilo Newton BPM 100 rocket engine for the speaker rocket has been slower than we hoped, we’re seeing a positive turn in our propulsion department.
Building a large-scale rocket engine to propel our crewed space capsule above the Karman Line to the edge of space has been a formidable challenge. But our team didn’t shy away from the difficulty of creating a single engine design that could carry the full weight of our four-ton speaker rocket, the largest amateur rocket ever built.
Through many trials and tribulations, we encountered the struggle of machining parts for such a substantial engine. The size of the BPM 100 engine components proved problematic, requiring us to reach out to external partners and confront issues of export control and dual-use items. These complexities slowed our progress.
Then, on a dark winter evening, an idea sparked within our team: what if we made a smaller engine? Within just a few hours, the team had outlined the possibilities for a smaller 25 kilonewton engine. A BPM 25 engine would be simpler to produce, with most parts being manufactured in-house. The engine’s smaller size meant that we could regain control over the production process and timeline.
While one BPM 25 engine does not equal the thrust of a BPM 100, we realized that we could cluster multiple engines to achieve the desired thrust. Although this approach comes with its own challenges, it also brings significant advantages, especially in terms of production efficiency.
With most parts for the BPM 25 engine already machined, we’re excitedly looking forward to completing the welding and stacking processes, along with the creation of the injector flange and injector pre-drilling tests. Once these steps are complete, we’ll have a new 25 kilonewton liquid propellant locks ethanol engine at our disposal.
In the near future, we will delve deeper into the pros and cons of the switch from BPM 100 to BPM 25 and share more about the machining and welding process. Your continued support makes our progress possible, and we are excited about the journey ahead. Stay tuned for more updates as we get one step closer to space!